Bastin Hall houses cutting-edge technology that links the present with the lessons learned from the past. Here, Capt. James Bezjian, Ph.D., assistant professor of strategy and entrepreneurship in the Tommy and Victoria Baker School of Business, continues the legacy of the Monuments, Fine Arts, and Archives program. A division of the U.S. Army tasked with finding and recovering art and other priceless artifacts confiscated by the Nazis during World War II, the program was responsible for the recovery of cultural artifacts worth billions of dollars. In 2014, the Monuments program captured the attention of the public with the release of the film Monuments Men, starring George Clooney, Matt Damon and Bill Murray, which tells the story of how cultural treasures were protected and rescued by Allied forces.
This past summer, Bezjian completed Army Monuments Officer Training through the Smithsonian Cultural Rescue Initiative and the U.S. Army Civil Affairs and Psychological Operations Command (Airborne). Almost 80 years after the founding of the program and the deployment of the original Monuments Men, Bezjian echoes his predecessors’ core beliefs: “If we want to become better versions of ourselves as humans, the only way to do that is to learn from the mistakes of the past. And we can’t do that without preserving the history of humanity. Doing that means making a concerted effort, not just to preserve icons but to preserve stories that people pass down from generation to generation and preserve the history of groups and tribes and individuals who have grown up in various regions with different ethnic and socioeconomic backgrounds.”
Preservation, Bezjian believes, is key to ensuring that history is not misremembered. “Until all that stuff is documented, recorded and preserved,” he said, “it stands to be lost or twisted or changed or manipulated. Preserving culture prevents us from making the mistakes of the past, and it also prevents people from twisting a narrative.”
In February 2020, Bezjian and a couple of cadets traveled to the U.S. Army Airborne & Special Operations Museum in Fayetteville, North Carolina. They used 3D technology to create digital replicas of war artifacts, including an Army-issued M1 steel helmet worn by Walker Hancock, an original member of the Monuments Men.
Bezjian’s next mission, sponsored by an $8,500 contribution from the Richard Lewis Foundation, is to rescue art not from the hazards of war but from the decay of time, specifically to preserve the Madonna of La Gleize in Belgium.
Bezjian’s carry-on, an Artec Leo 3D scanner, too precious to check, is already packed in its protective case, awaiting the international flight. Bezjian will scan the Madonna at its home church in Belgium and bring the scans back to The Citadel, where he will print the sculpture twice in polylactic acid plastic using a 3D printer. The printer itself was created and donated by Benjamin Scott, ’21, and Ethan Warner, ’20, who submitted it as their entry in the 2020 Baker Business Bowl, the school’s entrepreneurial business plan competition, and subsequently launched Evolve 3D, a company that manufactures 3D printers and develops 3D printing technology.
One of the two replicas will then catch a flight to Belgium, where it will be housed with the original. The other replica will trace Bezjian’s earlier journey to the Airborne & Special Operations Museum, where it will be featured in an upcoming exhibit.
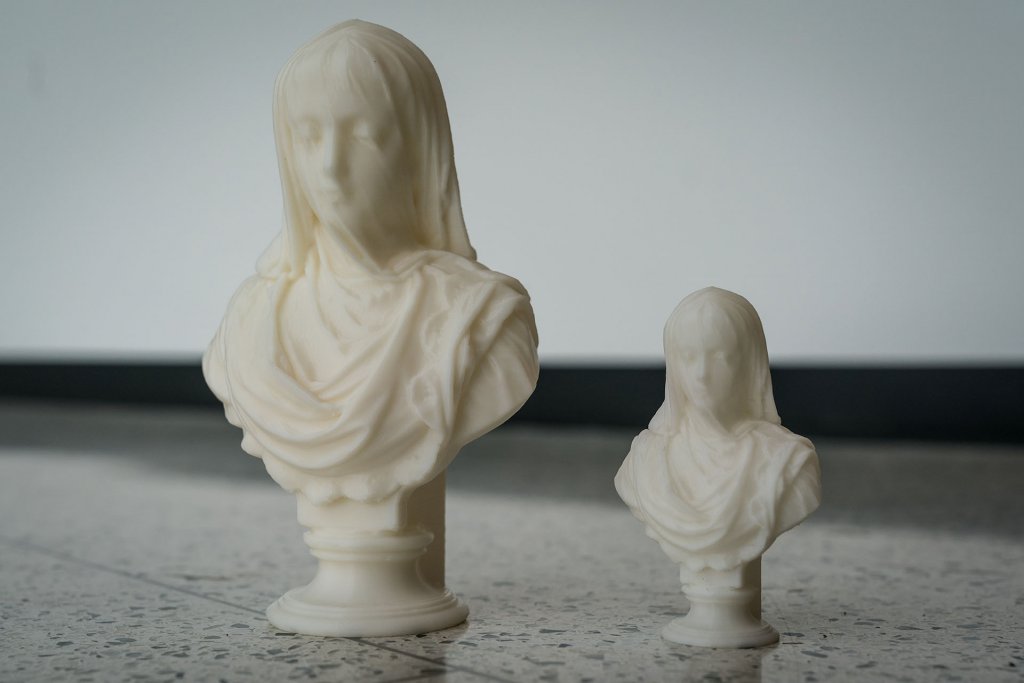
“The goal behind any kind of cultural heritage preservation is to capture not necessarily the icon, but the meaning that the icon has for our community,” said Bezjian.
The Citadel’s 3D printers work layer by layer, and since the Madonna replicas will be reproduced to scale, they might have to be printed in segments due to the sculpture’s height. The segments could then be melted or glued together. The depth of each layer and the number of layers needed will not be known until Bezjian’s team begins fabrication using Artec software. At that point, he will also choose a brand of polylactic acid plastic made from renewable resources and decide whether to use an infill for added structural support. In any case, he does not expect the replication process itself to cost more than a few hundred dollars. After the fabrication is completed, an artisan will color and texturize the replicas’ surfaces to match the original sculpture.
As an example of the printing process’s precision, Bezjian keeps on his desk a miniaturized version of the Veiled Lady by Pietro Rossi, which is housed at the Gibbes Museum of Art in downtown Charleston. The lines on this 3D-printed plastic replica softly and delicately drape across the bust’s face the same way the rock-hard marble does on the original, forecasting the success of the forthcoming to-scale replicas of the Madonna.
The scanning and printing process captures minute details, revealing not only the artist’s technique but also the sculpture’s history, and will allow Bezjian to create a precise replica of the Madonna, including any damage incurred during World War II, when it was stolen by the Nazis.
“You want to create a 100% pure replica from the time that it was scanned. So the goal is essentially to take a snapshot of what that sculpture looked like at that date and time.”
Just as we are to remember and learn from our successes, we should remember and learn from our scars. The lessons from artwork like the Madonna of La Gleize will be preserved and shared as a result of this project and others to come.